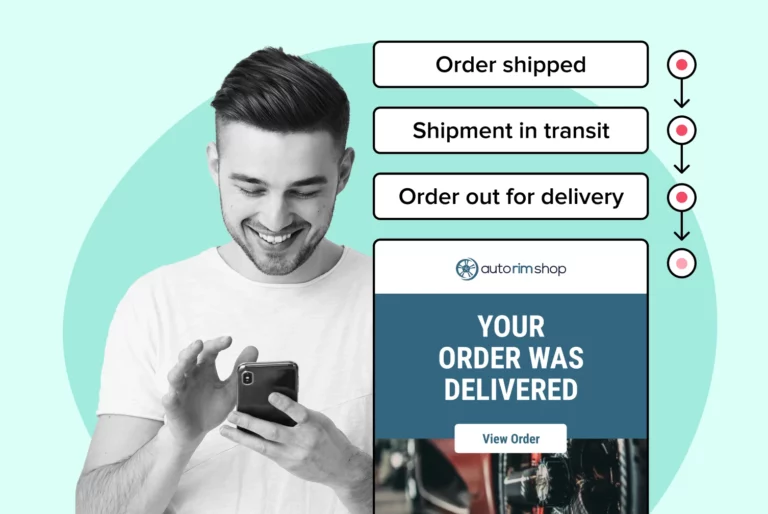
What is Outbound Logistics and how to use it?
This blog post explores outbound logistics in e-commerce, its challenges, and optimization best practices.
Shipping, Tracking & Notifications
Boost customer experience and reduce support tickets
Realtime order and shipment tracking
Proactive order and shipping notifications
AI-Enhanced Discounted Labels
Predictive pre-purchase estimated delivery dates
Self-Serivce branded order tracking
Effortless experience delivered
Identify and Resolve Order Issues
Realtime order and shipment tracking
Make returns profitable and delight customers
Flexibility to define any return destinations & conditions
Simplify returns for your customers and team
Incentivize exchanges over returns
Returns management made easy for your team
Returns management made easy for your team
Easy claims and smart upsells
Understand why your customers are returning
In-Store & Curbside Pickup
Unify the online and the in-store experience
Hassle-free pickup experience for customers
In-Store dashboard to keep operations streamlined
In-Store and Online orders unified
Drive foot-traffic to your stores
Shipping, Tracking & Notifications
Boost customer experience and reduce support tickets
Realtime order and shipment tracking
Proactive order and shipping notifications
AI-Enhanced Discounted Labels
Predictive pre-purchase estimated delivery dates
Self-Serivce branded order tracking
Effortless experience delivered
Identify and Resolve Order Issues
Realtime order and shipment tracking
Make returns profitable and delight customers
Flexibility to define any return destinations & conditions
Simplify returns for your customers and team
Incentivize exchanges over returns
Returns management made easy for your team
Returns management made easy for your team
Understand why your customers are returning
In-Store & Curbside Pickup
Unify the online and the in-store experience
Hassle-free pickup experience for customers
In-Store Dashboard to keep operations streamlined
In-Store and Online orders unified
Drive foot-traffic to your stores
Boost customer experience and reduce support tickets
Realtime order and shipment tracking
Proactive order and shipping notifications
AI-Enhanced Discounted Labels
Predictive pre-purchase estimated delivery dates
Self-Serivce branded order tracking
Effortless experience delivered
Make returns profitable and delight customers
Flexibility to define any return destinations & conditions
Simplify returns for your customers and team
Incentivize exchanges over returns
Returns management made easy for your team
Equip your team for precise return checks.
Understand why your customers are returning
Unify the online and the in-store experience
Hassle-free pickup experience for customers
In-Store Dashboard to keep operations streamlined
In-Store and Online orders unified
Drive foot-traffic to your stores
Find the answer to all your questions
Take a step by step trip through our functionality to see how we can improve your ecommerce processes.
Explore the most comon questions about WeSupply
Calculate the ROI that WeSupply can bring you
Request a no strings attached review of your current shopping experience and missed conversion opportunities
Read actionable articles on how to optimize your post-purchase experience and decrease support tickets
Get inspired by stories of how our customers implemented an effortless post-purchase experience
Wondering if WeSupply is a good fit for you? Read through our use cases to see how we can help you increase conversion & improve CX!
A Deep Dive into Top Companies' Order Tracking & Returns Strategy
Find the answer to all your questions
Explore the most comon questions about WeSupply
Calculate the ROI that WeSupply can bring you
Request a no strings attached review of your current shopping experience and missed conversion opportunities
Take a step by step trip through our functionality to see how we can improve your ecommerce processes.
Read actionable articles on how to optimize your post-purchase experience and decrease support tickets
Get inspired by stories of how our customers implemented an effortless post-purchase experience
A Deep Dive into Top Companies' Order Tracking & Returns Strategy
Wondering if WeSupply is a good fit for you? Read through our use cases to see how we can help you increase conversion & improve CX!
Have you ever wondered how eCommerce businesses fulfill customer orders efficiently and accurately? The answer lies in an essential document called a pick list. These lists hold the key to streamlining the order fulfillment process and ensuring customer satisfaction. So, what exactly is a pick list, and how can it help your business? Read on to discover the world of pick lists, their components, and how they contribute to the smooth operation of warehouses.
In this comprehensive guide, we will explore the definition of a pick list, its importance in warehouse management, and the various types of pick lists available. We’ll also dive into the essential elements every pick list must-have, and how Warehouse Management Systems (WMS) play a crucial role in pick list management. Let’s start our journey into the world of pick lists!
Pick Lists are an important source for efficient and accurate order fulfillment.
Optimized pick lists contribute to customer satisfaction and operational efficiency through accuracy, expedited order fulfillment, scalability, and other benefits provided by Warehouse Management Systems integration.
Advanced techniques such as batch, zone & wave picking offer businesses the opportunity to optimize their warehouse operations & enhance customer satisfaction.
While Pick Lists are an important part of the eCommerce process, a post-purchase optimization software like WeSupply can help you take it to the next level. By effortlessly providing real-time tracking for orders and shipments, delivering timely order updates, forecasting delivery dates before purchase, and integrating with an extensive global carrier network. This ensures that customers remain well-informed and content throughout their buying experience.
A pick list is an authoritative source that determines the order and all personnel involved in the fulfillment process in a warehouse. This includes shipment details, item-related information and warehouse location. All of this is necessary for warehouse personnel to safely and systematically process and dispatch orders. In short, a pick list functions as a guide for warehouse staff to orderly and efficiently fulfill customer orders.
Pick list systems are closely linked to warehouse organization systems, as they help determine the most efficient picking method for fulfilling customer orders. There are various methods for creating pick lists, such as:
Printing out each order as it arrives
Utilizing a spreadsheet for organizing picklists
Implementing a WMS system to generate the necessary pick lists in a safe and controlled manner.
The primary purpose of a pick list is to furnish the operator with all the instructions and requisite data to prepare and dispatch products securely and in an orderly fashion. An incorrect pick list can lead to sending customers the wrong products, resulting in wasted packaging and shipping costs. For this reason, the accuracy and efficiency of the operator picking the route should be confirmed.
A pick list comprises products that need to be packed and shipped to customers, thereby assisting warehouse personnel in efficiently fulfilling customer orders. For larger warehouses or businesses managing their own warehouse, a pick list may include additional information such as warehouse location.
The top section of a pick list includes details regarding the company producing the order, such as:
Order number
Date
Operator code
Warehouse location
Shipment type & number
A pick list can include a single item or a combination of items, such as five of one SKU and three of another. For each order, a pick list includes item details to pick, the quantity of each item, the location of the items, and a product image. Discrete pick lists and batch pick lists are two of the most common types of pick lists used in the eCommerce shipping industry. They are designed to make order fulfillment faster and more accurate.
The middle section of a pick list usually includes essential product details like aisle number, storage level, item description, units required and the remaining SKUs. It also helps ensure accuracy for obtaining items from their respective shelving units. The pick list has a bottom section which contains a space for recording comments and observations. There are also three signature boxes at the end, to be signed by the picking operator, the employee preparing the order after receiving it, and the dispatch authority respectively.
Optimizing pick lists has a positive impact on customer satisfaction by ensuring that orders are fulfilled accurately and efficiently. Additionally, it contributes to operational efficiency by simplifying the order fulfillment process and minimizing warehouse labor and operating costs. The traditional physical approach to pick lists involves manually picking items from shelves, while transitioning to digital pick lists offers advantages such as enhanced accuracy, expedited order fulfillment, and scalability.
Warehouse Management Systems (WMS) integration with pick lists offers benefits such as heightened accuracy, expedited order fulfillment, and scalability. By implementing best practices for pick list management, such as regularly monitoring and reviewing pick lists, empowering and training warehouse staff, and evaluating picking performance for ongoing optimization, businesses can ensure that their pick lists are accurate, efficient, and contribute to overall customer satisfaction and operational efficiency.
Additionally, you can further enhance the customer experience by utilizing post-purchase software such as WeSupply, which enhances customer satisfaction even further by streamlining every aspect of the experience once the order has been placed. WeSupply facilitates accurate real-time Order Tracking, Proactive Shipping Notifications and even provides the possibility of setting up a Self-Service Returns & Exchanges center to streamline and boost the efficiency of your returns process.
Answer the #1 Customer Service Question: Where is My Order?
Book a quick call with our experts to see how WeSupply can help you give customers the ability to track their orders on your website to decrease the number of WISMO support tickets.
A pick list should include the following essential elements:
Customer information and order details
Product details, SKU, and identifiers
Picking instructions
Notes and additional context
These components ensure that warehouse staff have all the necessary information to fulfill orders accurately and efficiently.
The succeeding subsections will delve into each of these elements and their importance in the picking process.
The customer details section of a pick list should include essential information such as the customer or company name, shipping address and key contact details. This ensures accurate and timely delivery of orders. Order date and time, as well as any associated deadlines, should be included. Order dates and times are extremely important for eCommerce businesses. These businesses frequently operate under service level agreements that mandate the dispatch of orders the same day they are placed.
Ensuring that the order number is consistent with the order numbers used on invoices, receipts, and customer’s records is of paramount importance. Including customer details on a pick list can prevent potential delays in case warehouse pickers require making substitutions or have queries.
For each item on a pick list, the following information should be listed:
Item name
Required quantity
SKU numbers or UPC codes to identify the specific product
Location of the product in inventory to ensure efficient picking.
Quantity is a critical component of the pick list and can easily be overlooked. The quantity should be clearly displayed on the pick tickets for anyone to easily comprehend how much of an item is being picked. As an alternative, utilize a WMS system that will alert the picker if the quantity is not accurate. The order number guarantees that items on the pick list are arranged in the appropriate order.
Including a photo of the item can expedite the shelf selection process and enhance order accuracy, inventory management, and return avoidance.
Clear picking instructions and additional context on pick lists can aid warehouse staff in accurately and efficiently picking the correct items. For example, including a photo of the item can help verify that the picker is obtaining the correct product.
Providing all necessary instructions, such as the stock keeping unit (inventory SKU), quantities, and location of items, helps warehouse operators gather items for customer orders. A pick list facilitates accurate reporting by enabling the user to select only one option without requiring any additional verification or input.
Including pictures and product descriptions can further enhance the accuracy and efficiency of the picking process.
Physical and digital pick lists each have their unique advantages and disadvantages. The traditional physical approach to pick lists involves manually picking items from shelves, while digital pick lists offer benefits such as enhanced accuracy, expedited order fulfillment, and scalability.
The subsequent subsections will scrutinize the differences between physical and digital pick lists, and discuss how businesses can shift from one to the other.
The traditional physical approach to pick lists involves manually constructing and administering pick lists on paper or other physical media, as opposed to those that are generated automatically.
Physical pick lists are:
Easy to use
Require minimal training
Cost-effective
Suitable for any environment
However, they are not as effective or precise as digital pick lists, which provide instant visibility into the picking process, leading to improved inventory management and order tracking.
Digital pick lists are an essential part of operations on the warehouse floor. They are used with mobile devices, tablets, and laptops. Order details are automatically allocated and sent to each picker, providing them with instructions on their device for an optimized process.
A digital picking list offers several benefits:
Reduces manual processes
Makes it easier to include additional data such as product images
Serves as a double check to ensure the picker gets the right item
Digital pick lists offer the following benefits:
Increased efficiency and precision
Real-time visibility into the picking process
Improved inventory management
Enhanced order tracking
To transition from physical to digital pick lists, it is recommended to:
Implement mobile devices, tablets, or laptops on the warehouse floor
Generate digital pick lists automatically instead of using physical paper
Utilize mobile scanners and tablets for completing the picking process
Ensure that order details are wirelessly sent to the mobile devices used by inventory pickers
Consider including images of the products in the digital pick lists for improved accuracy and efficiency.
These steps, when followed, can facilitate a smooth transition from physical to digital pick lists in your warehouse operations.
Various picking methods can help improve order fulfillment in your warehouse, such as batch picking, zone picking, and wave picking. Each of these methods has its unique advantages and can be employed to optimize pick lists and facilitate order fulfillment.
Each picking method and its benefits will be explored further in the following subsections.
Batch picking is a process of fulfilling multiple orders of the same item simultaneously. This method is highly effective for subscription-based businesses, as many customers receive the same products.
Batch picking reduces the amount of movement required by the pickers, resulting in improved efficiency and productivity.
Zone picking involves:
Assigning different personnel to designated areas of the warehouse
Each individual is familiar with their area
Working together to fulfill one pick list
This method is a cost-effective and time-saving approach to order fulfillment, as it requires fewer resources to complete orders and minimizes the potential for errors by limiting pickers to their designated zones.
Zone picking can also help to improve accuracy and reduce the amount of time spent on order fulfillment.
Wave picking is a method that combines the principles of zone and batch picking. Here’s how it works:
An operator collects a batch of items from one zone.
The operator then transfers the batch to the subsequent zone.
The pick list will show all the items that need to be taken from the current zone.
The pick list will also highlight items required from the subsequent zone for the orders.
Orders move through the warehouse in batches, like the rolling waves of a sea. Finally, they reach the packing station. Wave picking reduces the time spent walking around the warehouse and searching for items, thus improving efficiency and accuracy in the picking process as well as the picking packing stage.
A warehouse management system (WMS) plays a crucial role in pick list management by facilitating the integration of pick lists with other systems, such as inventory management and order fulfillment. This warehouse management system wms integration provides numerous benefits, including enhanced accuracy, efficiency, and customer satisfaction.
The subsequent subsections will highlight the benefits of WMS integration with pick lists and discuss considerations when selecting a WMS for your warehouse.
Integrating a WMS with pick lists offers several advantages, such as increased accuracy, efficiency, visibility into inventory levels, and customer satisfaction. In addition, a WMS can help to decrease picking mistakes, monitor inventory in real time, and expedite order fulfillment.
By integrating a WMS with pick lists, businesses can streamline their warehouse operations and enhance the overall picking process.
When selecting a WMS, it is important to consider the following factors:
The cost of the system
Its scalability
The features and capabilities it offers
The ease of use
The level of integration with other systems
The customer support offered
Taking these factors into account will help you make an informed decision when choosing a WMS.
By carefully evaluating these factors, businesses can choose the perfect WMS to enhance their pick list management, improve the accuracy of their picking process, and optimize their warehouse operations.
WeSupply stands as a pivotal post-purchase platform, elevating the customer shopping experience with features like real-time order tracking, accurate delivery forecasts, and integration with an expansive WMS and global carrier network. Beyond these, its in-depth analytics provide a window into the intricacies of logistics, shipments, and order management. Such insights empower businesses to make data-driven decisions, refining every step from when an order is placed to its successful delivery, ensuring consistent customer contentment.
Implementing best practices for pick list management can ensure that your warehouse operations run smoothly and efficiently. These practices include regularly monitoring and reviewing pick lists, empowering and training warehouse staff, and evaluating picking performance for ongoing optimization.
Following these best practices, businesses can maintain the accuracy and efficiency of their pick lists, thereby enhancing customer satisfaction and operational efficiency.
Regularly reviewing and updating pick lists is essential for guaranteeing accuracy and efficiency in order fulfillment. Additionally, it assists in recognizing any potential issues and making the necessary alterations to the pick list to maximize the picking process.
By regularly monitoring and reviewing pick lists, businesses can identify areas for improvement and make adjustments to enhance the overall picking process.
Equipping and training warehouse staff is of great importance as it can lead to a number of benefits, such as:
Increased productivity
Improved accuracy
Enhanced safety
Better customer service
Employee satisfaction and retention
Providing concise instructions, establishing attainable objectives, and furnishing feedback and appreciation are recommended methods for empowering and training warehouse staff. Investing in staff development and empowerment enables businesses to optimize their picking processes and ensure efficient operations.
In cases in which there are multiple warehouses, they may be trained or equipped to deal with different types of products or processes. With WeSupply, you can benefit from the Intelligent Dispositions functionality to ensure that returned products make it back into the warehouse best equipped to handle and restock or recycle them, ensuring the empowerment and training your warehouse staff has received are used to their maximum potential.
Evaluating picking performance is vital for continuous improvement, allowing businesses to:
Identify areas needing improvement
Make the necessary adjustments
Assess the effectiveness and accuracy of the picking process
Optimize their operations
Minimize mistakes
Augment productivity.
This assessment assists in recognizing bottlenecks, executing process enhancements, and improving overall performance. Regular assessments of picking performance can help businesses identify and address any issues, leading to continuous improvement in warehousing operations.
The future of picking and the role of advanced techniques in warehousing is promising. Techniques such as batch picking, zone picking, and wave picking are gaining traction in warehousing operations due to their improved efficiency and accuracy.
Furthermore, the integration of Warehouse Management Systems (WMS) with pick lists is becoming more commonplace, offering a range of benefits. By embracing these advanced techniques and implementing best practices for pick list management, businesses can optimize their warehouse operations, enhance customer satisfaction, and drive continuous improvement in the ever-evolving world of warehousing.
As we conclude this comprehensive guide on pick lists, you may still have some lingering questions or concerns. This bonus section will answer some common questions and provide additional insights into pick lists, assisting you in better understanding and implementing this crucial tool in your warehouse operations.
In summary, pick lists play a vital role in the efficient and accurate fulfillment of customer orders in warehousing operations. By understanding the different types of pick lists, their essential components, and the various picking methods available, businesses can optimize their warehouse processes and enhance customer satisfaction. Furthermore, leveraging advanced techniques and Warehouse Management Systems (WMS) in pick list management can provide numerous benefits, driving continuous improvement in the ever-evolving world of warehousing. So, take this knowledge and apply it to your business, ensuring that your warehouse operations run smoothly and efficiently, with pick lists at the heart of your success.
WeSupply is a transformative post-purchase platform designed to elevate the eCommerce experience. Complementing traditional pick lists, it integrates seamlessly with WMS and a vast global carrier network, offering real-time order tracking, proactive shipping notifications, and precise delivery forecasts. Additionally, WeSupply provides a self-service center for returns and exchanges, streamlining the process. Its deep analytics dive into logistics, shipments, and order management, empowering businesses to make informed decisions that enhance every facet of the customer journey, from order placement to delivery, ensuring customer satisfaction.”
Picklists are documents that contain all the necessary information to fulfil customer orders, such as item description, storage location and quantity. Pickers use the list to find the requested items in order to meet the customer’s needs.
Drop-down menus have a shorter list of defaults than the pick-list, which can display up to 200 records. If you need to select an item that isn’t available in the drop-down menu, then the pick-list is the better option.
A pick list is a document sent to your warehouse pickers to fulfill a customer order. It provides them with the list of items needed, including their SKU, quantities and location in the warehouse. Pick lists can be created manually or using warehouse management system (WMS) software.
Creating a list in Excel is easy. Simply use the Data Validation tool under the Data tab and then create a custom list by clicking File > Options > Advanced > General > Edit Custom Lists, entering each entry into the List entries box, and clicking Add when you are finished.
A pick list is essential for successful order fulfillment, containing customer information and order details, product details, SKU, and identifiers, as well as picking instructions, notes, and additional context.
Have other questions?
Book a quick call with our experts to see how WeSupply can help you with pre-purchase delivery prediction, automated shipping tracking, proactive notifications and self-service returns.
Learn How To Create Successful Post Purchase Email Campaigns
Build an effective post-purchase email flow that helps you increase customer satisfaction and drive revenue growth!
This blog post explores outbound logistics in e-commerce, its challenges, and optimization best practices.
In this blog post, we will explore the importance of dunnage across various industries, its many forms, and the benefits it offers.
In this post, we’ll delve into first-mile delivery and strategies for enhancing supply chain performance and customer satisfaction.
So, what is the best multi-carrier shipping software, and why should your business consider implementing it? Let’s dive in!
In this blog, we’ll discuss eCommerce reverse logistics, helping retailers balance profit and customer satisfaction.
This article will delve into the concept of backhaul in eCommerce, and provide practical tips for successful implementation.
Discover effective e-commerce return solutions that enhance customer satisfaction and streamline processes!
The world of reverse logistics: the best reverse logistics companies providing these services in 2023 & how your business can stay ahead.
In this blog post, we’ll dive deep into the world of wardrobing, and discuss various tactics to mitigate its impact and protect your future profits.